Getting Lean: Waste Reduction in the Supply Chain
- andym10000
- Mar 23, 2018
- 3 min read
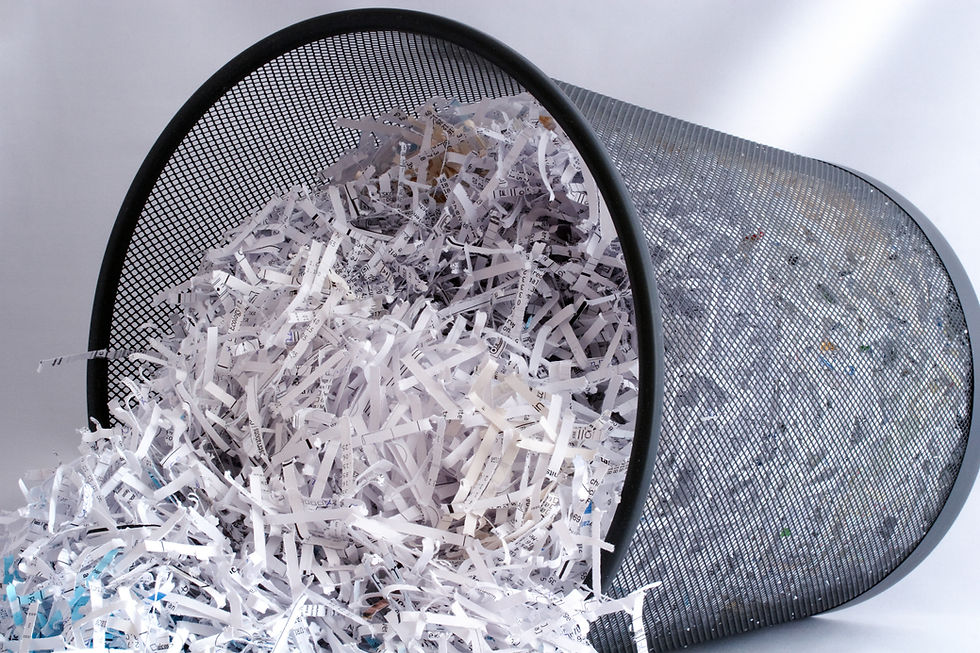
The ultra-lean manufacturing supply chains of Japanese automakers are often cited as model examples of low-waste supply chains. Progress Procurement examines if this still holds true and investigates how lessons from 'lean' can be applied across wider supply chain scenarios.
The ethos of lean is providing the customer with value sooner. It is clearly more than new processes.
Though numerous studies have shown that lean is a significantly more efficient and effective way to run a manufacturing operation, a large survey found that whilst 70% of US manufacturers attempt to employ it, only 2% of firms were satisfied with the results it brought.
Furthermore, many companies which implement lean fail to stick to the principles in the long term in spite of huge implementation efforts and costs.
So why is it so difficult to put lean into effect?
It has been observed that within Toyota factories, whilst many principles and ideas from lean are present, they are not replicated in the same way from plant to plant.
Factories are not instructed what to do by practitioners or experts and audited to see if they are following the best practices.
Instead, a learning culture is instilled in the factories. The result is many incremental steps towards lean, some of which are abandoned and others embraced.
This results in differing practices throughout Toyota because different manufacturing operations have learned in different paths. Toyota is continually recognised as the highest profile success story for lean supply chains, so the incessant standardisation that often accompanies lean implementations is clearly not a necessity. Indeed, it may be a key reason that implementations ultimately fail.
The key responsibility for managers is not to impart a routine for doing work, but to inspire habits and mindsets for continuous improvement.
Commonly, CPOs or COOs incentivise managers to execute certain initiatives to achieve a certain level of measurable improvement. It can quickly become an exercise of gutting existing ways of working with no sustainability and no continuous improvement.
Applying lean to varied supply chains
One of the key activities within lean is waste reduction within the category supply chain. Perhaps most valuable in manufacturing, this is a tangible way for procurement and supply chain professionals to add value across all industries and sectors.
Taiichi Ohno identified waste as a cost in the supply chain and devised a framework for identifying and eliminating it within the manufacturing context. Also known as TIMWOOD, some common examples are shown below:
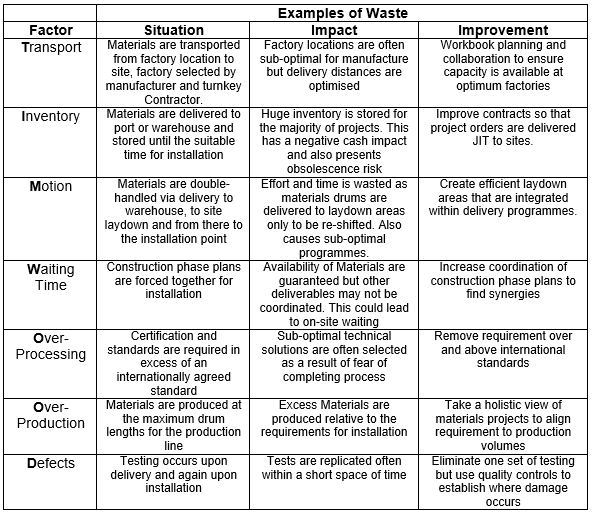
The model helps to identify some key improvements that could be made to reduce waste within the category. In the example, waste is abundant. Most strikingly, high value inventory is held, often for long periods. This waste in particular can contribute to significant cost in the supply chain.
Procurement practitioners should balance this with the ability to bundle requirements to best leverage their volume in the market, as these often conflict.
Defining the optimum order quantities can be best derived on conjunction with key suppliers, especially if the purchase requires manufacturing lines to be specially configured. If the cost of this can be ascertained, the relative cost of holding inventory can be calculated against the saving to determine the optimum order quantities.
Consideration should be given to the impact of stock levels on the relative risk of a stock out causing a stand down on site due to late supply, as the consequential costs to organisations could outweigh any benefits from inventory reduction.
By applying TIMWOOD to their whole supply chains and identifying where incremental, continuous improvements can be made to reduce waste, Procurement and Supply Chain Managers can enjoy the value from one of the core principles of lean without the often painful implementation issues.
Comments